Monday, March 31, 2014
What Are the Causes of Intermittent Car Ignition Problems

A bad ignition switch that intermittently goes off can cause a vehicle to die while youre driving. This can be dangerous, especially in heavy traffic. Having information on intermittent car ignition problems can be beneficial to automobile owners.
Causes
A couple of things that can cause an automobile to experience intermittent ignition problems. Sometimes these issues happen because you have a faulty ignition coil. However, the problems can also stem from a failed crankshaft position sensor.
Ignition Check
When experiencing intermittent car ignition problems, you and an assistant can perform a spark check in an effort to identify the problem. If the motor has spark plug wires, they should be taken off and placed beside the engine block. As your assistant starts the engine, your job is to check for a spark, because failure of the wire to produce a spark indicates a faulty ignition system.
Shock Warning
During the spark check with your assistant, you will need to be caul, especially after the vehicle has been started. You should make no contact with the wires, because if the ignition system turns out to be in working order while youre touching them, you could receive an electric shock.
How to Change the Front Wheel Hub in a 1998 Intrigue
The front wheel hub assembly on a 1998 Oldsmobile Intrigue contains both the bearing, hub, and wheel studs. This wheel hub assembly is non-repairable and must be replaced as an entire unit. Symptoms of a faulty hub assembly include a noticeable vibration that increases with vehicle speed, grinding or buzzing when turning, and howling or whining at speeds above 45 miles per hour. The hub assembly is secured to the steering knuckle with three steel bolts. These bolts must be replaced when installing the new hub assembly.
Instructions
Removal
- 1
Apply the parking brake and chock the rear wheels. Remove the hub cap on the affected side by loosening the hub cap locking caps with a 19 mm socket and a ratchet. Break the lug nuts loose with a 19 mm lug nut wrench.
2Raise the vehicle with an automotive jack and support it with two jack stands, one on each side. Check to make sure the vehicle is securely supported before proceeding.
3Remove the lug nuts with a 19 mm lug nut wrench and remove the tire. Have an assistant depress the brake pedal and loosen the axle shaft nut one revolution with a deep-well axle nut socket and a ratchet.
4Place a C-clamp over the brake caliper so one end of the clamps is over the rear side of the caliper and the other end of the clamp is over the outer brake pad. Loosen the caliper bleeder screw with a flare nut wrench, then tighten the C-clamp to compress the caliper piston. Tighten the bleeder screw immediately after compressing the piston.
5Remove the bolts holding the brake caliper bracket to the knuckle and pry the caliper and bracket off of the rotor together. Tie the caliper and bracket assembly to the strut spring with a piece or wire.
6Remove the brake rotor. Place a pry bar in between the wheel studs to hold the hub still, then remove the axle shaft nut. Loosen the three bolts on the back side of the steering knuckle that hold the hub assembly in place with a ratchet and metric socket. Install a two-jaw puller onto the hub flange. Center the puller screw on the end of the axle shaft. Tighten the puller screw to force the splined portion of the axle shaft out of the hub assembly.
7Remove the puller from the hub assembly. Remove the bolts that hold the hub assembly to the steering knuckle and remove the hub assembly from the vehicle.
Installation
- 8
Clean the circular hub assembly mating surface on the steering with a wire brush to remove any excess corrosion. Apply a light coating of grease to the axle splines. Slide the axle into the new hub assembly and rotate it until the three mounting holes align with the holes in the steering knuckle.
9Reinstall three new hub assembly mounting bolts with a ratchet and metric socket. Torque the bolts to 96 foot-pounds with a torque wrench.
10Set the brake rotor into position on the new hub and install two lug nuts to hold it in place. Slide the brake caliper and bracket into position over the rotor and reinstall the brake caliper bracket bolts. Tighten the bracket bolts to 137 foot-pounds using a torque wrench. Have an assistant hold a pry bar in between the axle nut studs to immobilize the hub, and then install a new axle nut on the axle spindle and torque it to 118 foot-pounds. Double-check to make sure that the brake caliper, bracket, hub assembly, and rotor are properly installed before proceeding.
11Reinstall the wheel and tighten the lug nuts using a lug nut wrench. Lift the vehicle off of the jack stands with an automotive jack and set it on the ground. Torque the lug nuts to 100 foot-pounds with a torque wrench and reinstall the hub cap.
12Pump the brakes until the pedal firms up; because the piston was driven back into the caliper bore, you must pump the brakes to move the piston forward into contact with the brake pads before operating the vehicle. Road test the vehicle to ensure that hub assembly and brakes operate properly.
Sunday, March 30, 2014
How to Remove the Spark Plugs on a 2002 Chevy Malibu
The spark plugs on your 2002 Chevy Malibus 3.1-liter engine thread into the cylinder heads just below the valve covers. There are three spark plugs on each cylinder head. If you are replacing the spark plugs, be sure to only remove one at a time and replace it with a new one before moving to the next plug.
Instructions
- 1
Open the hood of your Malibu and locate the negative battery cable on the battery terminal. Loosen the clamp bolt on the cable end with a wrench, then remove the cable from the battery. Set it aside.
2Locate the spark plugs on the right and left side of the engine. Select one of the spark plug wires and grasp the boot at the spark plug. Twist it slightly and pull it off the spark plug. Lay the wire aside.
3Install a spark plug socket over the spark plug, attach a ratchet to the socket, then rotate the socket and plug counterclockwise. Lift the socket and spark plug out of the cylinder head. Repeat the process for all six spark plugs.
Mercury Mystique Problems

Problems with Mercury Mystique vehicles have led Ford to initiate recalls for manufacturing defects affecting the vehicles brakes, steering column and seat belts. Registered vehicle owners should have been notified in 1999 or 2000 about these recalls.
Brake Problems
In March 2000, Ford recalled 436,200 vehicles including Mercury Mystiques equipped with anti-lock braking systems. The systems had a manufacturing defect that could cause the rear brakes to corrode and eventually malfunction, increasing the risk of a crash.
Seat Belt Problems
In August 2000, Ford recalled 144,435 Mercury Mystique vehicles because the seat belts did not meet federal safety standards. This could result in the passenger not being fully restrained in the event of a crash.
Ignition Switch Problems
In March 1999, Ford recalled 4,569 vehicles including Mercury Mystiques with automatic transmissions that utilize a park/lock solenoid due to a defect that could require replacement of the steering column. The defect made it possible that the the driver could turn the ignition key into the lock position and remove the key without the shift lever and transmission being in "park" mode, which could cause a crash and/or result in personal injury.
Saturday, March 29, 2014
How to Change a Head Gasket on a Dodge Shadow 2 5 Liter Engine
The Dodge Shadow was a compact car that Chrysler produced from 1987 to 1994. It had a variety of engine options, including a four-cylinder 2.5-liter Premier engine. This engine uses a single cylinder head, and you must replace the gasket each time you remove the cylinder head. The procedure for changing the cylinder head gasket is generally the same for all versions of the Dodge Shadow with a 2.5-liter Premier engine.
Instructions
- 1
Open the fuel filler cap to relieve the pressure in the fuel tank. Disconnect the wiring harness for the fuel injectors from the throttle body. Attach a jumper wire from the first terminal of the harness to a ground point on the engine.
2Attach one end of another jumper wire to the second terminal of the harness. Touch the other end of the jumper wire to the positive terminal of the battery positive post for five seconds to relieve the pressure in the fuel system. Disconnect the jumper wires, and disconnect the cable from the negative battery terminal with a socket wrench.
3Remove the radiator cap, and start the engine. Turn the heater on, and allow the engine to idle until the upper radiator hose gets hot. Stop the engine, and place a container under the radiator drain cock on the bottom of the radiator. Open the drain cock with a socket wrench, and drain the coolant into the container. Fasten the drain cock.
4Detach the accessory drive belt from its pulleys. Disconnect the mounting bolts for the air compressor with a socket wrench, and push the compressor aside to obtain access to the cylinder heads. Secure the compressor in place with cord.
5Disconnect the upper radiator hose and heater hoses from the engine. Remove the cover for the rocker arms, and disconnect the mounting bolts for the rocker arm with a socket wrench. Pull the rocker arms and push rods from the engine block. Disconnect the intake manifold and exhaust manifold from the engine block.
6Remove the mounting bolts for the cylinder head with a socket wrench. Lift the cylinder head from the engine block, and remove the cylinder head gasket. Remove any traces of the old gasket from the cylinder head and engine block with a gasket scraper.
7Cut the heads off two of the cylinder head mounting bolts, and cut slots in one end of each bolt to serve as alignment dowels. Install the alignment dowels into the number 8 and number 10 mounting bolt holes. Place the new gasket for the cylinder head onto the alignment dowels with the numbers on the gasket facing up.
8Place the cylinder head on the engine block and install the mounting bolts. Tighten the head bolts to 22 foot-pounds with a torque wrench on the first pass, then tighten them to 45 foot-pounds on the second pass. Tighten bolts 1 through 6 to 110 foot-pounds, tighten bolt 7 to 100 foot-pounds and tighten bolts 8 through 10 to 110 foot-pounds.
9Install the rocker arms and push rods to their original position on the engine block. Install a new gasket for the rocker arm cover, and replace the cover. Attach the hoses to the engine, and fasten the mounting bolts for the air compressor. Tighten the mounting bolts to 20 foot-pounds with a torque wrench.
10Mount the accessory drive belt to its pulleys, and adjust the tension on the belt. Attach the cable for the negative terminal with a socket wrench, and fill the radiator with coolant. Start the engine and check for fluid leaks.
Where Is a Camshaft Sensor in an Engine

A camshaft sensor notifies a vehicles ignition module so it knows which of the engines cylinders is properly positioned to be fired. The location of camshaft sensors can vary. Having information on the location, as well as other facts regarding camshaft sensors, can benefit vehicle owners.
Location
Because a camshaft sensor may be magnetic, it will often be found positioned directly on the timing cover located over the gear of the camshaft. It can also be located either inside a special type of housing that takes the place of the distributor, or inside the distributor itself.
Functions
Some vehicle engines have distributorless ignition systems. When this is the case, a camshaft sensors role is to notify the motors control module of the position of the camshaft as well as the crankshaft. The information taken from the camshaft sensor is then used to assist with proper ignition timing.
Diagnosis
Many vehicles model year 1995 or newer can be checked for camshaft sensor problems using a scan tool. Once it is plugged in, the scan tool reveals certain fault codes if there is a problem. For example, fault code P0342 indicates low input in the camshaft sensors circuit.
Friday, March 28, 2014
How to Repair Wiper Blades With Rubbing Alcohol

Continuous buildup of dust and debris such as dust, smoke and mineral deposits from rain water reduces the efficiency of the windshield wiper blades on your car. Poorly performing wiper blades create hazardous driving conditions when its raining, potentially leading to accidents or even death. Performing frequent wiper blade maintenance significantly improves the efficiency with which the wipers remove dust, debris and water from the windshield and saves the cost, frequency and hassle of purchasing and installing new windshield wiper blades.
Instructions
- 1
Pour 1 cup of rubbing alcohol into a measuring cup.
2Soak 10 cotton balls in the alcohol until the cotton balls become saturated with alcohol.
3Pull the windshield wipers away from the windshield to allow yourself easy access to the blades for cleaning.
4
Wipe one cotton ball along the entire length of the wiper blade. Discard each cotton ball after it is used. Repeat the process as many times as necessary until the liquid runs clear from the wiper blade.
5
Soak a soft linen cloth in a solution of 50 percent rubbing alcohol and 50 percent warm water. Wash the windshield surface from top to bottom to remove dust, dirt, oil and other grime from the windshield and improve the performance of the wipers.
Explanation of a Parallel Pin Punch

Removing a locking pin from a drive shaft or pulley can be tricky without the right tools. A parallel pin punch makes removing pins a simple task for engineers and mechanics.
Description
A parallel pin punch is a solid metal punch with a striking plate at one end. The opposite end of the punch is turned to a specific diameter. The sides of the punch are not tapered. Parallel pin punches are available in variety of sizes, and may have a rubberized grip or a guard to protect the hand from poorly aimed hammer blows.
Use
Choose a parallel pin punch with a diameter matching the pin to be removed, and place the punch on the end of the pin. Grip the punch firmly and strike the end with a hammer. Loosening the pin beforehand with a tapered punch makes the parallel punch easier to align and prevents damage to the end of the punch.
Alternative Uses
Parallel pin punches can be used to align holes in metal plates or other objects, provided that the holes are of equal diameter and run parallel to each other. A parallel pin punch may also be used as a peg to hold multiple holed plates in alignment while drilling or tapping occurs. Parallel pin punches are used in woodworking to drive a nail further into a surface without impacting the surrounding wood.
Thursday, March 27, 2014
How to Reset the Dodge Ram 3500 Computer

You can reset the computer on your Dodge Ram 3500 right from your home garage or driveway, saving yourself time and money. The Dodge is equipped with an on-board diagnostics computer that monitors all functions of the vehicle. Sensors positioned throughout the Dodge Ram 3500 send trouble codes to the computer when they sense a malfunction. The computer illuminates warning lights and service lights on the instrument panel to alert you to have the vehicle looked at and repaired by a qualified mechanic. Once the repairs have been made, you need to reset the computer to turn off the warning and service lights.
Instructions
- 1
Pop up the hood of your truck and hold it open with the rod. Locate the battery. On the batter is the negative battery cable clamp with a nut on it. Loosen the nut with an end wrench.
2Remove the negative cable clamp from the battery, taking care not to touch the positive side of the battery with it.
3Let the vehicle sit for 30 minutes. Put the negative cable clamp back onto the negative battery terminal and tighten the nut with the end wrench.
4Put the key into the ignition and turn over the engine. Examine the instrument panel to make sure all service and warning lights have shut off. If so, the computer has been reset.
Tips on a Delco Alternator

Delco-Remy began manufacturing alternators more than a century ago, and has packed that 100 years of experience and improvements into a component part used in machinery ranging from automobiles to windmills. Despite Delcos efforts, problems with alternators do occur
Bad Connection
If the battery in your vehicle is discharging, but the alternator tests good at a repair facility, the problem may be a bad connection. Remove corrosion and grime at the mounting points, since rust and grease will block an electrical current. Clean the terminals of your alternator thoroughly, and clean the connectors of the power output wires. The online automotive advice service AA1.com advises doing these checks before looking at anything else to eliminate one of the most overlooked problems -- a poorly grounded alternator.
Sensing Trouble
Listen and look to detect trouble in the alternator. Turn the engine on. Listen for whining or screeching noises coming from the alternator. If you hear screeching, make sure the source of the noise is the alternator, and not a loose belt. If the belt is tight, turn the engine back on. Noise from an alternator indicates the bearings are bad. Turn the engine off. Look at the alternator closely. Look for burn or scorch marks on the rear vents. This indicates the alternator is burning out. Smell (yes, smell) the alternator. If you smell a slightly sweet burned smell almost like burnt sugar, the alternator is burning out.
If either condition is present, disconnect the battery. Disconnect the alternator wires, and remove the alternator. You can take it to a garage for further evaluation if youre not sure if there is a problem, however its best to replace the alternator if any of the conditions are present. Rebuilding an alternator requires tools and knowledge normally beyond that of the average home mechanic.
One-Wire System
No need to get confused because your Delco alternator only has one wire. Many Delcos are called "one-wire" because they have just one output wire. The control circuitry is built into the alternator, eliminating the need for outside voltage regulation. To install, just ground the casing, which is the negative. The single red wire is positive and must connect to the positive terminal of the battery.
Wednesday, March 26, 2014
How to Replace a Steering Gear

A steering gear controls an automobiles movement and should be properly maintained on a regular basis. To find out whether you need to replace your steering gear, check the condition of the fluid and hoses. If the fluid is contaminated or the hoses are worn, replace the steering gear immediately before taking the vehicle out on the road. Check a shop manual specific to your vehicle for correct specifications.
Instructions
- 1
Disconnect and cover both of the fluid lines to stop any leakage or contamination. Mark and disconnect the steering shaft coupler. The steering shaft can only be completely removed once the steering gear is taken out.
2Raise the vehicle on a car lift. Use a wrench to remove the Pitman arm from the shaft. If you dont have a car lift, then a car jack and jack stands will work just as well.
3Use a wrench to remove the mounting bolts holding the gear case to the frame. Slide the steering gear away from the car. Take the steering shaft out of the vehicle.
4Mount the new gear casing into the frame and secure it in place with the mounting bolts. Align the Pitman arm to the shaft and tighten it in place with the wrench.
5Attach the coupler to the steering shaft and connect it to the gear casing. Reconnect the two fluid lines and replace the fluid. Find a quiet road to test the steering gear before taking the vehicle out on a busy thoroughfare.
How to Adjust a Rear Brake Pedal on a Harley Road Glide

The original equipment connection between the rear brake pedal and the rear brake master cylinder on all Harley-Davidson Road Glides to date is completely mechanical and not hydraulic. The mechanical connection is the same whether your Road Glide is equipped with your original brake pedal or an aftermarket pedal.
Instructions
- 1
Sit down next to the right side of your motorcycle and find the brake pedal.
2Find the rear brake master cylinder which is approximately parallel to the bottom of the brake pedal and about two feet closer to the rear of the bike. Then find the metal rod that connects the two.
3Loosen the jam nut that connects the rear brake cylinder to the brake rod by turning the nut counterclockwise with an open end wrench.
4Turn the brake rod with an open end wrench fitted to the flattened section of the brake rod. Turn the rod clockwise to lower the pedal and counterclockwise to raise the pedal.
5Tighten the jam nut by turning it clockwise when the brake pedal is adjusted to the proper height.
6Inspect the cotter pin that locks the brake rod to the brake pedal assembly. Use pliers to replace the cotter pin if it is broken or very corroded.
Tuesday, March 25, 2014
Where Is the MAF on a 1989 Mustang

Midway through the 1964 model year, Ford released the first of the "pony cars," the Mustang. The release of this vehicle prompted Chevrolet to follow suit in 1967 with the release of the Camaro. In the late-1980s the Mustang began using more electronic components to control the engine. One of these components is the mass air flow sensor, which is commonly called the MAF sensor.
Location
Both the 5.0-liter and the 2.3-liter Mustangs had the same location for the mass air flow sensor, about halfway between the air box and the engine on the air intake tube. It is a metal cylinder with a wiring harness plugging into it.
Tools
The mass air flow sensor attached to the air intake tube by a simple hose clamp. Depending on the style of hose clamp, either a ratchet and socket, flathead screwdriver or Phillips screwdriver will be all you need to replace it. To properly test a mass airflow sensor, use a digital volt/ohm meter.
Function
The mass air flow sensor works by using a hot ire sensing unit to measure the temperature of the air coming into the engine and a cold wire to sense the ambient temperature. The air passing over the heated wire causes it to cool. The mass air flow sensor then compares the temperature of the cold wire to the heated wire and sends that information to the vehicles computer. The computer uses that information to determine the air-to-fuel ratio in the combustion chamber.
Cleaning
On occasion the hot and cold wires are simply dirty and cannot take proper readings. When this occurs, you can clean the wires with parts cleaner to restore them to their proper operating condition. Use caution not to damage the wires though.
Testing
Check that the voltage getting to the mass air flow sensor is at least 10.5 volts. To test the sensor operation, you must check the voltage at the vehicles computer. The sensor should read approximately: .60 volts at idle, 1.10 volts at 20 mph, 1.70 volts at 40 mph and 2.10 volts at 60 mph.
Replacement Procedures for a 2001 Avalon Thermostat
A faulty thermostat can cause a number of problems, such as engine overheating and reduced cooling system efficiency. Although the thermostat is a small, inexpensive component, its absolutely critical to the proper operation of a liquid-cooled engine. The 3.0-liter engine in a 2001 Toyota Avalon contains a thermostat thats designed to open at a temperature of 176 to 183 degrees Fahrenheit. The most common thermostat fault is a failure to open. In this situation, the thermostat valve doesnt open when it should, preventing coolant from properly circulating and causing the engine to overheat.
Instructions
Removal
- 1
Allow the engine to cool for at least two hours to prevent burns and other injuries related to the high temperate of the engine and engine coolant.
2Raise the vehicle with a jack and support it with jack stands. Remove the radiator cap and place a drain pan underneath the radiator. Loosen the drain valve with a ratchet and metric socket. Allow the coolant to drain out until the stream flowing from the radiator slows to a drip. This may take 30 minutes or more. Close the radiator drain valve. Place the drain pan under the engine, beneath the thermostat housing.
3Remove the bolts holding the V-bank cover in place at the top of the engine with a 5 mm hex wrench. Remove the bolts holding the air cleaner hose and resonator in place with a ratchet and metric socket. Then remove the air cleaner assembly from the vehicle.
4Squeeze the spring clamps holding the heater hoses to the water inlet with a pair of pliers and slide them down the water hoses. Pull the heater hoses off of the water inlet.
5Disconnect the coolant temperature sensors electrical connector. Remove the nut holding the wire protector to the water inlet with a ratchet and metric socket and remove the protector from the inlet.
6Remove the bolts holding the water inlet pipe to the water inlet with a ratchet and metric socket. Remove the water inlet pipe from the water inlet.
7Remove the nuts holding the water inlet to the cylinder head, then remove the water inlet from the cylinder head. Remove the thermostat from the inlet.
Installation
- 8
Install a new gasket onto the new thermostat. Set the water pump inside the cylinder head opening so that the small jiggle valve on top of the in line with the top-center water inlet valve mounting stud.
9Set the water inlet valve onto the cylinder head so the cylinder head studs pass through the holes in the water inlet. Install the water inlet nuts and tighten them to 69 inch-pounds with a torque wrench.
10Remove the old O-ring from the water inlet pipe. Install a new O-ring on the water inlet pipe and coat it with soapy water. Install the water inlet pipe into the water inlet, then install the water inlet pipe mounting bolt into the cylinder head and torque it to 14 foot-pounds with a torque wrench.
11Set the engine wire protector into position and reinstall its retaining nut with a ratchet and metric socket. Reconnect the coolant temperature sensors electrical connector.
12Connect both heater hoses to the water inlet. Squeeze the spring clamps with a pair of pliers and slide them down the hoses and release the pliers when they are in their original position.
13Set the air cleaner and resonator assembly into position and reinstall its retaining bolts. Set the V-bank cover into position and reinstall its retaining bolts with a 5 mm hex wrench.
14Fill the radiator with a 50/50 mixture of Toyota Long Life Coolant and distilled water until it reaches the top. Replace the radiator cap and fill the coolant reservoir with the same mixture until it reaches the FULL mark. Start the engine and allow it to come up to operating temperature. Check for coolant leaks and then re-check the coolant level. Add coolant if necessary to raise the coolant level to the FULL mark on the side of the coolant reservoir.
Monday, March 24, 2014
How to Rebuild the EMPI in a Carburetor
The carburetor on a vehicle is used for the internal combustion inside the engine. This works by mixing the fuel with air to create the combustion that propels the engine while driving. A European Motor Parts Incorporated carburetor kit allows you to replace any worn or leaking parts in your carb. These kits can be used with everything from a VW Beetle to a 78 Chevy. If you would like to rebuild your carburetor with an EMPI kit, you can do it with little hassle. You dont have to be an auto mechanic to rebuild your carburetor; you can do it yourself even if you have minimal knowledge of the task.
Instructions
- 1
Buy an EMPI carburetor kit. This can be found at local auto parts stores or through an online outlet. EMPI kits come with all of the rubber seals and gaskets that you need to rebuild your carb.
2Put on safety glasses and gloves to keep grease and dirt off of your hands and out of your eyes. Remove the carburetor from your vehicle. Consult your service manual if you do not know how to remove the unit, as the process can vary from car to car.
3Look over the diagram that came with your EMPI kit. This diagram will vary depending on the carburetor kit specific to your vehicle. Use a ratchet to remove the accelerator pump from your carburetor. Remove the cover from your carb and then remove the choke linkages as well. All of these parts are labeled on the diagram that comes with your EMPI kit.
4Use a stiff-bristled toothbrush and cleaner to remove all debris from the parts on your carburetor. Use the EMPI kit diagram to replace the broken parts on your carb. Put the carburetor back together and then reinstall the carburetor in your car.
Sunday, March 23, 2014
How Do I Replace an O2 Sensor in a 1998 Chevy Blazer

The 1998 Chevy Blazer has three oxygen (O2) sensors. Two are located up on the front Y-pipe bolted to the V-6 engines manifold. These two sensors detect the fuel-to-air mix in the exhaust and transmit that information to the powertrain control module (PCM). From there, the PCM makes adjustments to achieve the lowest emissions possible while still running properly. The last O2 sensor is located after the catalytic converter. This sensors job is to monitor the efficiency of the catalytic converter.
Instructions
- 1
Apply the parking brake to lock the rear wheels.
2Open the hood to the 1998 Chevy Blazer to allow some light down into the engine compartment. This will be helpful when under the vehicle to replace the front oxygen sensor(s). If you are replacing the rear sensor, opening the hood is not necessary.
3Lift one front side of the Blazer up high enough to rest it on a jack stand and then lift the other side and rest that side on a jack stand.
4Put on the safety glasses and crawl underneath the Blazer to locate the oxygen sensor(s) being replaced. One is located on the left-side Y-pipe up near the manifold connection, the other is on the right-side Y-pipe near the manifold and the rear sensor is located in the catalytic converter pipe just behind the shell of the converter.
5Unlock the wire harness plug from the O2 sensor plug. Use the small screwdriver to press inward and release the lock while pulling the O2 sensor plug and wire away from the wire harness plug.
6Spray penetrating oil around the threaded connection of the O2 sensor where it screws into the O2 sensor port of the exhaust piping. Allow the oil a few minutes to soak in.
7Thread the O2 sensor wire through the closed end of the 22 mm wrench and then place the closed end of the wrench onto the sensors hex-head. Turn the wrench to the left (counterclockwise) to remove it from the port. Remove the sensor.
8Inspect the threads of the replacement sensor. Most will come with a light coating of special anti-seize compound already on the threads. Some O2 sensor manufacturers will provide a small tube inside the box. If applying the compound, be sure to avoid getting the compound on the thimble-tip of the sensor. Only place a small amount on the threads of the sensor.
9Thread the sensor into the port by hand to avoid crossing the threads of the sensor. Tighten the sensor with the wrench after threading the wire through the closed end again. Only tighten the sensor snugly. Over-tightening the sensor risks stripping the threads of the sensor and/or possibly damaging the threads to the sensor port.
10Connect the replacement sensor wire plug to the wire harness plug before crawling out from under the Blazer with the tools and old sensor(s) and lowering the vehicle.
How to Replace the Timing Belt on a 2005 KIA Spectra
The Kia Spectra is a compact car produced from 2000 to 2009. The second generation of this series includes the 2004 through 2009 models, and represents a major redesign over the first generation Kia. The only engine available for the 2005 Kia in North American is a four-cylinder 2.0-liter engine with a double overhead camshaft. This design uses a timing belt to drive the camshafts with the crankshaft. The most important part of replacing the timing belt is keeping the crankshaft and camshafts in the correct position during the procedure.
Instructions
- 1
Disconnect the cable from the negative battery terminal with a socket wrench to ensure you dont inadvertently start the engine. Raise the vehicle and support it on jack stands. Remove the engine cover, right wheel and side cover for the right wheel. Detach the accessory drive belts, water pump pulley and upper cover for the timing belt.
2Turn the crankshaft pulley clockwise to align the groove on the pulley with the timing mark on the lower timing belt cover. Disconnect the pulley and flange for the crankshaft with a socket wrench. Remove the lower timing belt cover and timing belt tensioner. Detach the timing belt from the pulleys.
3Turn the crankshaft clockwise to align the timing marks for the crankshaft and camshaft. Install the timing belt tensioner with a socket wrench. Place the new timing belt onto the crankshaft sprocket, idler pulley, camshaft sprockets and timing belt tensioner in that order.
4Turn the timing belt tensioner clockwise to apply tension to the timing belt. Press the tension side of the timing belt with moderate force. The tension is correct when the deflection of the timing belt is about 0.2 in. Tighten the mounting bolts for the tensioner to 20 ft. lbs. with a torque wrench. Turn the crankshaft clockwise by two full turns and align the timing marks once again.
5Attach the lower timing belt cover and tighten its mounting bolts to between six and seven ft. lbs. with a torque wrench. Connect the flange and pulley for the crankshaft. Tighten the bolt for the crankshaft pulley to between 123 and 130 ft. lbs. Connect the upper timing belt cover and tighten the mounting bolts to between six and seven ft. lbs.
6Install the water pump pulley and accessory drive belts with a socket wrench. Attach the right wheel and side cover for the right wheel. Replace the engine cover and connect the cable to the negative battery terminal with a socket wrench.
Saturday, March 22, 2014
How to Remove Front Seats on a Ford Escape
Removing the front seats from your Ford Escape may be necessary if the seats need replacing, the carpet need to come out, or if you wish to replace the seats with aftermarket models. Damage to the seats or tracks can make them unstable, making safety of the seats a concern or affecting their comfort. Replacement seats are available from the Ford dealer or through some specialty auto-parts suppliers.
Instructions
- 1
Locate the seat adjuster on the outside edge of the seat. Move the seat all the way forward, then locate the two retaining bolts that secure the seat track to the floor behind the seat. Remove both bolts with a socket and ratchet, setting the bolts in a safe place for reuse later.
2Move the seat to the rear until it is all the way back, then locate the front mounting bolts under the seat. Remove the bolts from the floor and mounting brackets with a socket and ratchet. Set the bolts aside for now.
3Raise the front of the seat and locate the wiring harness connection under the seat. Depress the locking tab on the connector and separate the wiring harness pigtail from the connection on the base of the seat.
4Lift the seat and caully remove it through the door opening. Set it aside, keeping it off the ground, in a dry location. Repeat the process to remove the second seat from the front of your Escape, if required.
How to Install a Thermostat in a 2002 Grand Caravan

If the thermostat in the 2002 Dodge Grand Caravan malfunctions, the engine may not warm up properly and you may not be able to heat the cabin of the vehicle. This is annoying for the driver and passengers, especially if the thermostat fails in the winter. If the thermostat fails, replace the thermostat as quickly as possible to prevent extended use of the vehicle without proper engine heating.
Instructions
- 1
Drain two gallons of radiator fluid from the radiator via the petcock on the bottom of the radiator. You can reuse the fluid later so use a clean container.
2Locate the thermostat by following the upper radiator hose from the radiator to the housing on the engine.
3Pry the clamp off the hose with a pair of pliers. Pull the hose off the housing.
4Remove the bolts that secure the housing to the Caravans engine with a socket and ratchet. Pull the housing off the engine.
5Pull the thermostat out of the engine. Remove and discard the thermostat gasket.
6Clean the surface of the thermostat housing and the engine with a clean towel.
7Install the new gasket. Put the new thermostat into the hole.
8Place the thermostat housing on top of the gasket. Thread the bolts into the housing with your fingers. Tighten the bolts with the socket and ratchet.
9Slide the hose onto the housing. Secure the hose with the clamp.
10Pour the radiator fluid back into the radiator.
Friday, March 21, 2014
How to Install an Electric Fuel Pump in a 1997 Ford 7 3
A 1997 Ford vehicle may have a variety of engine sizes, including an 8-cylinder 7.3-liter diesel engine. This engine is in the larger pickup trucks, such as a F-250 or F-350. The 1997 Ford 7.3-liter engine uses fuel injection and requires a high-pressure electric fuel pump. The fuel pump in a Ford diesel engine is accessible from the engine compartment and its replacement requires you to first relieve the pressure in the fuel system.
Instructions
- 1
Disconnect both ground cables from the battery with a socket wrench to prevent accidental sparking from the battery. Loosen the filler cap for the fuel tank by 1/2 turn to relieve the pressure in the fuel tank. Open the filler cap completely.
2Raise the vehicle with a floor jack and support it on jack stands. Locate the electrical connector for the fuel pump in the engine compartment. It is behind the fuel pump and next to the frame rail. Detach the electrical connector from the fuel pump.
3Locate the retaining clip for the fuel line to the fuel pump. Slide the retaining clip off of the quick connect fitting for the fuel line. Remove the fuel pumps fuel line from the fuel pump with the fuel line tool.
4Remove the clips for the brake line from the bracket of the fuel pump. Disconnect the pinch bolt on the mounting bracket with a socket wrench and spread the bracket open. Detach the fuel pump from its mounting bracket.
5Install the new fuel pump by performing steps one through four in reverse order. Start the engine and check for fuel leaks.
How to Remove an LS1
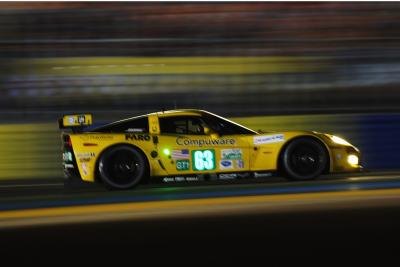
The LS1 engine is a small block motor produced by Chevrolet used in sports cars, sedans and SUVs. Engine removal becomes necessary when a car sustains body damage exceeding its value, but the engine is preserved, or when a swap is performed. The LS1 has high horsepower output, economical gas mileage and is light weight, making it a popular engine for car owners upgrading to a larger motor. Executing an LS1 removal requires expert knowledge in automotive mechanics to avoid engine and component damage.
Instructions
- 1
Unhook the battery, using a combination wrench to loosen the terminal bolts. Unclip the engine wiring harness, including any sensors and component connections. If reusing the wiring harness, ensure no dirt enters the wiring connections.
2Drain the radiator into a drain pan and remove the radiator and heater-core hoses with a screwdriver. The LS1 is a large engine and the working space is cramped. Remove the radiator fans, air bridge and radiator by unbolting the mounting bolts with a socket set to provide engine removal room.
3Drain the engine oil into a drain pan by removing the oil-drain bolt with a socket set. This prevents oil from damaging the top end of the engine during removal. Unbolt the exhaust manifolds and smog system, using a socket set. If the bolts are seized, apply penetrating oil and allow it to sit for 15 minutes before removing the bolts.
4Remove the air-conditioning system, using a pipe wrench to loosen the line connectors. If the air-conditioning system is charged, uncharge both the high and low pressure sides by depressing the service ports on each respective side with a screwdriver prior to removing the air conditioning lines. Remove the power-steering assembly, using a socket set. Use a drip pan to catch any power-steering fluid draining from the system.
5Unhook all vacuum hoses and the transmission-to-engine connections using a screwdriver and socket set. Unbolt the starter from the transmission, using a socket set, and remove the wires on the starter, using an adjustable spanner wrench. Place a jackstand under the transmission to support it after the engine is removed.
6Unbolt the transmission from the engine using a socket set and remove the dust shield. For automatic transmissions, remove the torque converter-to-flexplate bolts as well. Remove the valley cover by unbolting it with a socket set.
7Secure the LS1 to an engine tilt sling and attach the tilt sling to a chain rated for at least 800 lbs. Attach the other end of the chain to an engine hoist. Use four valley-cover bolts placed into the valley-cover bolt holes to attach the tilt sling directly to the engine. Place a washer between the chain mounts on the tilt sling and the engine block to prevent marring.
8Unbolt the engine mounts with a socket set. The engine is now free from the chassis and car. Tilt the front end of the engine up and hoist it out diagonally using the hydraulic jack on the engine hoist. Attach it to either an engine stand using the transmission-to-engine bolting points or place it on a used tire to prevent bottom-end damage.
Thursday, March 20, 2014
How to Install a Timing Belt on a 2002 KIA Rio Cinco
The Kia Rio is a subcompact car that Kia Motors has produced since 2001. The Cinco trim level of the Rio is a five-door hatchback available in the United States. The procedure for installing the timing belt depends only on the engine and is not directly affected by the trim level. The 2002 Kia Rio Cinco has a four-cylinder, 1.5-liter engine that uses a timing belt to synchronize the movements of the camshaft and crankshaft.
Instructions
- 1
Remove the cable from the negative terminal of the battery with a socket wrench. Detach the accessory drive belts from their respective pulleys. Disconnect the alternator and water pump.
2Disconnect the crankshaft pulley with a socket wrench and remove the guide plate from the timing belt pulley. Disconnect the upper and lower covers for the timing belt.
3Turn the crankshaft pulley clockwise to align the timing mark on the pulley with the timing mark on the engine. The I and E marks on the camshaft pulley must also align with their respective marks on the cylinder head. Disconnect the timing belt tensioner pulley and the timing belt with a socket wrench.
4Connect the pulley for the timing belt tensioner. Pull the tensioner away from the crankshaft pulley as far as possible and fasten the lock bolt for the tensioner to hold it in place. Place the timing belt onto the crankshaft pulley, idler pulley, exhaust camshaft pulley, intake camshaft pulley and tensioner pulley, in that order.
5Loosen the pulley for the timing belt tensioner to apply tension to the timing belt. Tighten the lock bolt to between 28 and 38 foot-pounds with a torque wrench. Turn the crankshaft clockwise by two full turns and align the timing marks.
6Install the upper and lower covers for the timing belt with a socket wrench. Tighten the mounting bolt for the crankshaft pulley to between 9 and 13 foot-pounds with a torque wrench. Connect the water pump pulley and tighten its mounting bolt to between 9 and 13 foot-pounds.
7Install the alternator and attach the accessory drive belts. Connect the cable to the negative terminal of the battery.
How to Drill Out a Broken Exhaust Stud

The bolts and studs used to assemble a vehicles exhaust system and connect it to the manifold are exposed to extreme temperatures while the engine runs. Because theyre on the underside of the body, theyre also constantly exposed to rain, ice and road salt. Given this operating environment, its sometimes a wonder exhaust studs dont always break while being removed.
When an exhaust stud does snap, however, there are a number of approaches to removing the broken shaft. Start with the first, and keep trying until the stud finally comes out.
Instructions
Heat Method
- 1
Expose the shaft of the broken stud. Check to see whether there is enough length for a secure grip with a pair of vise grips; if not, go to the next method.
2Heat the surrounding metal with an oxy-acetylene, propane or MAPP torch. Play the flame over the metal all around the stud, but do not heat the stud itself; you want to expand the metal holding the stud to make the bolt hole larger while leaving the stud its original size.
3Clamp a set of vise grips securely on the exposed end of the stud, and turn the stud counterclockwise. Do not apply excessive force, which might damage the stud further. If the stud moves slightly, apply more heat; if not, move to the next method.
Left-Hand Drill Method
- 4
Grind the exposed head of the stud flat with a grinder. This will help prevent the drill bits from slipping off center. Liberally apply penetrating lubricant to the broken stud.
5Punch a dimple at the center of the bolts surface with a hammer and metal punch. Drill a pilot hole into the center of the bolt with a 1/8-inch bit. Keep the hole centered and straight.
6Reverse the drill, and load a left-hand drill bit 3/16 to 1/8 inch smaller than the diameter of the stud. Drill straight into the pilot hole with the left-handed bit to avoid accidentally cutting the metal surrounding the threads.
7Allow the left-hand bit to loosen the stud by its own rotation. Repeat the process with a larger left-hand bit or bits until the stud comes free. Once free, lubricate the hole, and clean out rust. If the stud still will not come out, move to the next method.
Drill-Out Method
- 8
Choose a drill bit with a diameter slightly larger than that of the original stud, including its threads. The purpose of drilling a new hole is to remove all traces of the old, stuck stud.
9Drill straight down the center of the stud, following the previous holes, to the full depth. This method will remove the old, broken stud entirely while leaving a straight-sided hole larger than the original. Clean all rust and shavings from the new hole.
10Insert a thread repair kit such as a Helicoil in the drilled hole, following the instructions packaged with the kit. Use a replacement stud of the original size when reassembling the exhaust system.
Wednesday, March 19, 2014
How to Reset the ABS Light on a Ford

An ABS (anti-lock braking system) light will illuminate on your Fords dashboard when there is a problem with the braking system that need to be addressed. Take the vehicle to your mechanic to have it looked at and fixed. To clear the code from the On-Board Diagnostics computer, you need to reset it manually. This will just take a few moments. Make sure you fix the problem before you reset the light in order to ensure the light remains off after the reset.
Instructions
- 1
Put the key into the ignition and turn it to the second position. This is the position just before the engine starts.
2Open the hood of the Ford and loosen the nut on the negative battery cable clamp. You can do this with a 10mm wrench.
3Slip the clamp off the negative side of the battery and wait about 5 minutes.
4Put the clamp back in place and tighten the nut. Look on the dashboard to make sure the ABS light has turned off. This resets all lights in the car and the clock as well.
Does the Catalytic Converter Affect Fuel Economy
Catalytic converters are part of a cars exhaust system that reduce the amount of nitrous oxide produced by burning fuel. When working properly the converter should not affect fuel economy, but it can if it becomes clogged or damaged.
Exhaust Backpressure
If your cars catalytic converter becomes plugged or clogged, it restricts the airflow of exhaust from the engine. This causes more and more exhaust to build up in the engine which reduces the amount of new, combustible oxygen the engine pulls in. A common cause of a clogged catalytic converter is overheating due to a misfiring spark plug.
Diagnosis
When it is receiving less oxygen, the engine must work harder to achieve speed. This increased work lowers fuel economy, reduces power when driving at high speeds and can cause overheating and stalling. If your car runs normally for a few minutes after starting, but then begins to cough or sputter, your converter may be clogged. Especially if you have noticed other symptoms, have your mechanic check the cars exhaust backpressure.
Solution
If your catalytic converter is clogged or damaged, it will need to be replaced. Make sure to investigate the reason that the first converter was ruined so the replacement does not suffer the same fate.
Tuesday, March 18, 2014
My 87 Nissan Van Wont Start

Problems with a Nissan van starting can occur for a variety of reasons but the battery and the fuel levels are the primary reasons it will not start. Many people consult a mechanic when their cars will not start, but you can troubleshoot the issues yourself. Corrosion on the battery terminals, a dead battery, or no gas in the van will probably be the reason your Nissan van will not start.
Instructions
- 1
Pop the hood to the Nissan van and locate the battery next to the engine.
2Look the battery connections over for any corrosion. Use a socket wrench to loosen the terminal connections.
3Clean the terminals with soda and a wire brush and then connect the terminals back onto the battery.
4Try to restart the car. If the car does not start, jump-start the van with jumper cables and another car.
5Leave the van running for at least five minutes and then turn the car off. Try to restart the van. If the van does not restart, replace the battery.
6Add 1 gallon of gas to the van and then try to restart the van. If the van restarts, get a mechanic to repair your fuel gauge.
What Does a Ballast Resistor Do

The process of starting a car involves more than simply turning the key to fire up your engine. Between the battery and the starter, a ballast resistor helps regulate the voltage.
Definition
WordNet Search defines a ballast resistor, most commonly found in an automobile ignition system, as a device "inserted into a circuit to compensate for changes, [such] as those arising from temperature fluctuations."
Function
A ballast resistor helps regulate voltage flowing in an electrical system to avoid overloads or battery drainage.
Use in Automobiles
As the starter motor begins to crank the engine, it causes a significant drain on the battery. The ballast resistor allows the ignition system to operate at a lower voltage until the engine starts. After ignition, the alternator begins to recharge the battery, restoring the regular voltage. The ballast resistor then functions to regulate the voltage going to the ignition system to avoid additional wear on the system.
Additional uses
Low-voltage lighting systems, such as florescent, LED and neon lights, frequently contain ballast resistors.
Monday, March 17, 2014
Infinity Q45 Repair Procedures
The Infiniti Q45 is a Japanese-produced rear-wheel-drive automobile. In order to ensure operator safety and maximize the life of a car, all major repairs should be carried out by a qualified professional. The owners manual of the Infiniti Q45 includes several sections providing information on when repairs should be conducted by service professionals. For example, while punctured tires can be dealt with by the car operator, problems with the Infiniti Q45s complex airbag deployment system should be dealt with by a qualified professional.
Infiniti Q45
As of July 2011, the last model of the Infiniti Q45 was released in 2006. It features firm suspension tuning, a 4.5-liter V8 engine, an automatic transmission, 340 horsepower and 333 pound-feet of torque. The 2006 model featured active rear steering (which monitored vehicle speed and steering), 19-inch alloy wheels, a transmission with downshift rev-matching and a lane departure warning system.
Warning Lights
In many cases, the Infiniti Q45 tells drivers when certain features on the car need to be repaired through the use of warning lights. While some warning lights, such as the low-fuel warning light and the low tire pressure warning light, indicate problems that can be fixed by the driver, other warning lights indicate problems that must be attended to by a qualified professional. These include a seat belt warning light, an airbag warning light, a transmission warning light, a break warning light, a battery charge warning light and an engine oil pressure warning light, among others. If any of these lights come on, take your vehicle to a mechanic with the required knowledge.
Windshields
Windshields may be damaged in a variety of circumstances, such as a collision, an act of vandalism or stone being thrown up by other cars on the road. A cracked windshield is a significant safety hazard and must be replaced immediately by a qualified professional. In addition to the threat of shattering glass, a cracked windshield may also affect the deployment of the supplemental airbag system.
Airbags
The Infiniti Q45 owners manual contains a special section on repair procedures associated with its airbag system. If the airbag warning light comes on, the system may either need to be repaired or replaced. Due to the complexity of the system, the airbag system should only be checked by a certified mechanic. Anytime there is damage to the front or side of the vehicle, the airbag system should be inspected. Any time an airbag has been inflated, the airbag system should be replaced. When working under the hood or inside the vehicle, the ignition should always be in the "lock" position.
How to Use Muffler Clamps for a Leak in the Exhaust
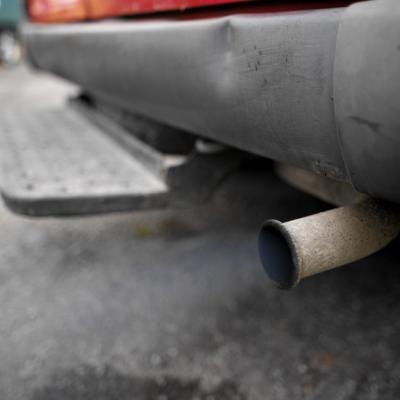
Exhaust leaks can be a pain to deal with because not only do they sound horrible, but they can be difficult to find. Once you do discover where the leak is, though, then you have to find a way to fix it, using whatever you can to get the job done. One option is to use a pair of muffler clamps to clamp a patch piece of metal or heat blanket around the exhaust, stopping it from leaking in the process.
Instructions
- 1
Lift up the vehicle using the jack and place it on jack stands. Make sure the vehicle is secure before you crawl underneath it.
2Crawl underneath the vehicle and locate the exhaust leak. Wrap the exhaust wrap around the tubing, making sure to cover the leak as well as any area 2 inches in front and behind of the hole, and keep the wrap tight. Cut off any excess tubing using scissors.
3Place a muffler clamp over one end of the wrap, and slide the base of the clamp onto the U-bolt, tightening it in place using the 3/8-inch ratchet and socket. Repeat this process with the other side of the exhaust wrap.
4Raise the vehicle off of the jack stands using the jack and place it back on the ground. Start the vehicle and check again to see if you hear the exhaust leak. If you do, consider adding another layer of exhaust wrap to fix the noise or look for additional leaks.
Sunday, March 16, 2014
How to Change the Tensioner Pully on a 94 Dodge Caravan
The tensioner pulley on a 1994 Dodge Caravan serpentine belt tensioner assembly allows the transference of tension from the tensioner to the belt. The pulley itself has an internal bearing ring so it can rotate freely at the end of the serpentine belt tensioner arm. If the bearing ring gives out, the pulley will either wobble or seize, neither of which is conducive to continued serpentine drive system operation. Unfortunately, the pulley itself is not serviceable. However, Dodge does offer the entire tensioner assembly. Anyone with good mechanical aptitude can change a Caravan tensioner in about an hour.
Instructions
- 1
Lift the Caravans hood and support it with the prop rod. Examine the belt routing diagram sticker, placed on the fan shroud or underside of the hood, to verify the location of the belt tensioner on your specific Caravan.
2Rotate the Caravans serpentine belt tensioner assembly clockwise to relieve the tension on the belt. Slip the belt off the tensioner with your free hand before rotating the tensioner back to its home position. Remove the tool.
3Extract the two mounting bolts that hold the serpentine belt tensioner assembly to the Caravans front engine cover using your socket set. Depending on your physical size and dexterity, you may find this easier to accomplish through the top of the engine well or through the passenger-side wheel well.
4Pull the old serpentine belt tensioner assembly out of the Caravans engine bay by hand. Place the new serpentine belt tensioner assembly on the Caravans front engine cover and bolt it in using your socket set.
5Rotate the new serpentine belt tensioner assembly clockwise with the serpentine belt tool and then place the belt on the pulley by hand. Rotate the new serpentine belt tensioner assembly back into place. Remove the tool and close the hood.
How to Ship Tires to an APO

APO (Army Post Office) addresses function almost exactly like standard post office addresses within the United States. In fact, the Military Postal Service Agency (MPSA) is an extension of the U.S. Postal Service (USPS) that aims to extend postal service to military and diplomatic personnel stationed overseas. Some limitations apply depending on the country to which you are shipping, but, generally speaking, sending an item to an APO address involves the same steps as sending the same item to a standard USPS address.
Instructions
- 1
Determine the exact APO address to which you want to ship the tires.
Based on the APO address, look up any relevant restrictions for the country or post to which you are shipping. Some APO stations are forced to restrict mail by contents, size or weight because of in-country complications, but most should be able to accommodate a shipment like tires. You can check for the latest restriction status at your local post office or at the USPS website.
2Package your tires.
Package the tires for shipment as you would any other parcel for international delivery, taking basic precautions to cushion the tires. If you are shipping to an APO address that has size limitations, consider sending the tires individually to fall within the size restrictions on parcels. Weight should not be a problem when shipping tires.
3Print the full APO address on the package in clear readable handwriting. Include the recipients full name, box or destination details, and APO number. The USPS offers the following address as an example of a complete and full entry:
SSGT Kevin Taylor
Unit 2050 Box 4190
APO AP 96278-2050
Be sure to also include your return address.
4Send your parcel to the APO from any U.S. post office. You will need to pay the applicable shipping charge for the delivery.
Saturday, March 15, 2014
Holley 9776 Specs
Holley is a manufacturer of fuel systems, and since 1903 the companys workers have made over 250,000 carburetors. These carburetors have been made for vehicles like Henry Fords original Model A, factory muscle cars, and WWII PT Boats and airplanes. The Holley 9776 carburetor is one of Holleys Model 4160 Adjustable Float carburetors.
Part Number, Product Line and Application
The 9776 carburetor is part of Holleys model 4160 four-barrel carburetors. The carburetors are meant for street and mild race vehicles, and they have vacuum secondaries with a metering plate that doesnt have accelerator pumps, power valves or jets. This means that the 9776 will be easier to tune than full race carburetors. The actual manufacturers part number of the 9776 carburetor is 0-9776 -- this number will come in handy if youre asking for information about it from a service technician.
Barrels, Flange, CFM, Choke and Fuel
The Holley 9776 carburetor has four barrels and a square bore carburetor flange. The CFM or cubic feet per minute -- a measurement of air volume velocity in the carburetor -- has been measured at 450. This carburetor does not have a choke and it uses unleaded gasoline for fuel and a single fuel inlet. It comes with a 3/8-inch flare tube fitting to connect to the fuel line and two hose fittings: a 5/16-inch hose fitting and a 5/16-inch swivel fitting.
Secondary, Finish, Ford Kickdown and Throttle Linkage
The Holley 9776 carburetor has a mechanical secondary, but it doesnt have a secondary accelerator pump circuit. The finish on the 9776 is dichromate, which gives the carburetor an orange-red color. The 9776 does not have a Ford kickdown, but it does have a universal throttle linkage.
How to Clean a Forklift Battery

You can use a forklift in a warehouse or a farm to transport large, heavy goods. Some forklifts operate solely on battery power, and others are gas-powered and use batteries to power lights and to assist with turning the combustion engines. You may have to clean the forklifts battery from time to time if it has overflowed or has gotten dirty from mud or oil spilling on it.
Instructions
- 1
Remove the battery from its case using a screwdriver. Place the forklift battery on a pallet or on the floor. Put on gloves and keep them on during the entire cleaning process.
2Check for damage or cracks in the battery. Check whether the battery acid has overspilled from inside the battery. The acid is highly corrosive and conductive, and it should never get on outside surfaces.
3Mix 5 oz. baking soda with 1 gallon water in a bucket. Add more baking soda if the battery is heavily polluted with acid. The baking soda will neutralize the acids on the battery. Rinse the battery with the baking soda mix immediately after noticing that it has overspilled. Use plenty of water to completely dilute and wash off the overspilled acid.
4Brush the battery with a wire brush to remove any other dirt from the batterys surface. Rinse the battery once again with plenty of water to wash off any remaining dirt.
5Replace the battery into its case.
Friday, March 14, 2014
How to Remove the Ash Tray in a 1994 Audi Cabriolet
The Audi Cabriolet, also known as the Audi 80, was manufactured from 1966 to 1996. This car was the precursor to the more modern Audi A4. As Audis premier mid-size sedan for many decades, the Audi 80 was among the manufacturers bestselling vehicles. Although this car was quite reliable, repairs still need to be made from time-to-time. When interior repairs need to be made, one of the first components that you need to remove is the center console. The first step in removing the center console is removing the rear half of the console, which requires removing the ash tray.
Instructions
- 1
Shift the vehicles transmission into park or first gear for vehicles equipped with a manual transmission.
2Shut down the engine and remove the key from the ignition switch.
3Depress the button on the parking brake lever and disengage the parking brake so the lever is horizontal.
4Sit in the drivers seat and grip the ash tray with your right hand, placing four fingers inside the ash tray with your thumb on the outside. Pull the ash tray out as far as it will go. Remove any ash or or debris from the ash tray, using a vacuum. Wipe the ash tray clean with a shop rag.
5Pull the ash tray up and out of the center console. To reinstall the ash tray, set it into position inside the ash tray slot and press down on it until it click into position.
How to Repair Sprinter Glow Plugs
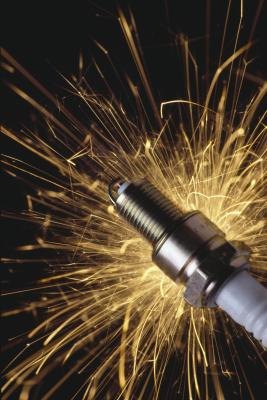
A Mercedes Benz Sprinter glow plug repair is a tricky endeavor but a necessary one particularly for owners in cold climates who want quick startups. The glow plugs are the diesel engines equivalent to spark plugs and an ignition system. Without properly working plugs, the Sprinter may not start. When one glow plug goes bad, odds are the rest of the plugs are going bad too. Save yourself some time and trouble by replacing all the plugs at the same time.
Instructions
- 1
Disconnect the battery as a safety precaution.
2Remove the injector lines, the injectors and the injector pump. Below the injectors are the heat shields that will need replaced. Remove the heat shields.
3Disconnect the buss bar. Beneath the buss bar, you will have access to the glow plugs. Use a socket or a box-end wrench to remove the glow plugs. Use the magnetic tool to pick up the plugs as the fit is tight and you may not be able to get your hands in to grab them.
4Apply the Teflon paste on the new plugs and install them. The magnetic tool will help you get the plugs into place, then use wrenches to tighten. Make the plugs snug but not overly tight. If you use a torque wrench, aim at about 15 pounds of torque.
5Replace the buss bar, then install the new heat shields. Replace the injector lines, injectors and injector pump. Use the anti-seize on the injectors to prevent future problems with disassembling. Tighten the injectors to about 55 pounds of torque.
6Start the Sprinter and check for leaks. The engine may be hard to start the first time. Continue to crank the engine until it starts. Double-check for leaks.
Thursday, March 13, 2014
PT Cruiser Service Guide
Chrysler released the first PT Cruiser in 2000. Classified as a sedan with a rear hatch, the 2010 PT Cruiser was the last of this model. Owners benefit from following the prescribed maintenance schedule within the PT Cruiser owners manual or service guide by increasing the vehicles life.
Oil Changes
According the 2010 Chrysler PT Cruiser owners manual, change the oil and oil filter every 3,000 miles or every three months if you frequently drive off-road, use your vehicle for a delivery service, drive on heavily trafficked roads or in an environment with temperatures frequently above 90 degrees Fahrenheit. Change the oil and oil filter every 6,000 miles in normal conditions or conditions not listed above.
Monthly Checks
Each month check your tire pressure and tire wear. Check the oil and fluid levels indicated by the engine oil dipstick, coolant reservoir and brake master cylinder. Also, test the light bulbs on the interior and exterior of the vehicle work.
Replacing Filters and Spark Plugs
Replace the spark plugs, air cleaner filter and make-up filter when the odometer reaches 30,000 miles, 60,000 miles and then every 30,000 miles thereafter in normal driving conditions.
Tricks for Removing a Rusted On Pulley From a Crankshaft

Nature finds ways to get rust onto old engines in the oddest of places. Every bolt, pulley or metal piece in an engine rusts at some point---even if embedded in an engine. Removing a pulley from the crankshaft already constitutes a difficult process. A visibly rusted pulley typically indicates that the rust goes into the engine, making the removal that much more difficult. Lubricants, air tools and specialty tools make the process easier.
Lubricants
Spray-on lubricants, such as spray silicone or liquid graphite, penetrate into pockets and holes in metal, reducing the coefficient of friction. A high level of friction makes a nut hard to remove. Rust increases the level of friction and degrades the quality of the nut. Soak the nut and the pulley thoroughly, and allow the lubricant to set in place for about 15 minutes. Scrub the nut with a wire brush to remove any topical rust, and respray the pulley.
Impact Wrench
The retaining nut holds to the crankshaft with high levels of torque. An impact wrench uses internal pistons powered by an air supply to hammer at a rotational gear. The hammering effect applies intense amounts of quick torque that will, after a few attempts, break almost any nut loose regardless of rust. You can also use a weaker electric impact wrench, but these will work less effectively against rusted metal. Remember to keep pressure against the nut as you activate the wrench.
Pulley Removal Tools
A pulley removal tool resembles a tripod with a bolt in the center. The tools feet hook under the pulley while you tighten the center bolt. Once you have removed the retaining nut, a pulley that has rusted onto the actual camshaft will still come free with the removal tool. The rust and pressure have created a cold-weld to the camshaft that you can break with high levels of force. The center bolt presses the camshaft inward while pulling outward on the pulley. You can use a normal socket wrench, but an impact wrench will make it easier to pop off the stubborn pulley, due to the vibrations caused by the impacts.
Wednesday, March 12, 2014
Why Does a Car Need Two Catalytic Converters

Catalytic converters were first put into use in the 1970s in response to the growing pollution problem in cities throughout the U.S. Today, all road-legal cars must, by law, be equipped with a catalytic converter and some even have two.
Function
Catalytic converters remove harmful elements from automotive exhaust by forcing the fumes to pass over metallic catalysts, including platinum, rhodium and palladium, which neutralize the toxins and transform them into relatively safe components. The entire casing of the converter is constructed of stainless steel. All of these expensive metals make a catalytic converter a costly piece of equipment.
Cars with Dual Exhaust
While most production cars have only one catalytic converter, some do come with two. Cars with dual exhaust often have two catalytic converters --- one for each set of pipes running from the headers to the rear of the vehicle.
Cars with Two In-Line Catalytic Coverters
Newer high-end vehicles are now coming equipped with two catalytic converters as part of an even more stringent emissions program. The first converter breaks down the exhaust as normal, while the second acts both as a filter for tiny particles and a pump which releases a chemical mixture that further reduces any harmful gases which may have escaped the first converter.
How to Adjust a Parking Brake in a 95 Mx 5

You can adjust the parking brake on your 1995 Mazda MX-5 right from your home garage, saving time and money. You will know that its time to adjust your parking brake when the vehicle starts to slip when parked downhill. Adjusting the parking brake takes up the slack in the parking brake cable, allowing the parking brake to be more effective. You only need a few basic tools to do the job.
Instructions
- 1
Start the engine. Step on the brake pedal so it goes all the way to the floor four times. Shut off the engine.
2Locate the center console cover between the drivers and passengers seats. Unhinge the hooks. Remove the cover by lifting up.
3Find the adjuster nut attached to the parking brake cable. Tighten the nut with the wrench.
4Lift up on the hand brake one click. Start the engine and look on the instrument panel to see that the parking brake light is on. Disengage the hand brake.
5Put wheel chocks behind and in front of the front wheels. Lift up the rear end of the Mazda with a jack. Slide jack stands under the vehicle next to the two rear wheels. Lower the vehicle onto the stands.
6Spin the rear wheels forward with your hands. If youve done the adjustment correctly, they should spin freely.
7Raise up the vehicle, slide the jack stands out of the way and lower the car to the ground. Remove the jack and wheel chocks.
Tuesday, March 11, 2014
How to Identify GM Gen III Engines

GM Generation III small block engines, also known as LS1s, made their debut in the 1997 Corvette. According to "Engine Builder" magazine, Generation IIIs replaced the LT1 series. They have a smaller block, are lighter in construction and generate more horsepower than LT1s. Identifying Generation III engines is similar to other GM engines; begin visually, then locate the engine block casting number to be thorough. Although the LS1 identifies the engine family, it actually consisted of the LS 1 through 7, the L89 and C33. Truck versions of the Generation III were called "Vortec."
Instructions
- 1
Determine if the year and make of the vehicle are possible Generation III candidates. According to LS1 Engine, Generation III engines were used in 1997 to 2004 Corvettes, 1998 to 2004 Camaro SS and Z28 models, 1998 to 2002 Pontiac Firebirds, the 2004 Pontiac GTO and numerous GM Truck, van and SUV applications.
2Inspect the engine compartment. GM often put identifying decals and tags on the engine itself or in the compartment area. These may indicate the use of a Generation III engine. Also try to determine if the block is aluminum or cast-iron. According to "Hot Rod" magazine, most automobile LS1s were aluminum, while truck versions were cast-iron. Aluminum blocks will have a smooth finish as opposed to the rough grain of cast-iron.
3Locate the casting number on the engine block. "Hot Rod" places it on the drivers side, just below the cylinder head. It is an eight-digit number.
4Decode the casting number by comparing it to a casting number listing, similar to the one found on Fastnuf (see Resources). This listing will give the specifics of the engine in question when matched to the casting number.
How to Install Vance Hines Exhaust on a Harley Davidson Rocker

The Rocker is Harley-Davidsons custom chopper. With its solo seat, fat rear tire and kicked-out front end, it looks like it has been stripped down for speed. It actually weighs about 700 lb., however, and the engine produces only about 63 horsepower. Vance & Hines is one of several aftermarket exhausts. The Vance & Hines exhaust should boost your Rockers horsepower above 70.
Instructions
- 1
Cover all finished areas on the right side of the motorcycle with rags to protect your paint and chrome. Remove the right foot peg and brake pedal with a socket wrench. Loosen all of the fasteners that connect your exhaust manifold and exhaust support bracket with a socket wrench or box wrenches. Disconnect the two oxygen sensors with a wrench. You will reinstall these sensors with your new exhaust.
2Loosen all remaining fasteners holding the exhaust on by hand. Remove the old exhaust. Remove and replace the exhaust manifold gaskets. Using a small screwdriver or snap ring pliers, remove and set aside the clamps and retainer rings. You will use them on your new exhaust.
3Install all of the hose clamps that will support the heat shields. They must remain loose. If you tighten the hose clamps at this point, you risk warping your exhaust.
4Use a wrench and thread locker to bolt on the new exhaust mounting bracket that came with your Vance & Hines pipes.
5Reinstall your retainer rings and clamps in your new exhaust. Loosely bolt your new exhaust to your exhaust manifold and exhaust support bracket. Put Teflon paste on the oxygen sensors and reinstall them in your new header pipes.
6Tighten the bolts that attach your new exhaust to the exhaust headers and support bracket using a wrench. Attach your heat shields to the hose clamps with a flat-head screwdriver.
Monday, March 10, 2014
How to Install a Headlight on a 2007 Caliber

There are some vehicles that are somewhat easy to replace headlights on. Unfortunately, the 2007 Dodge Caliber (and many other Dodge vehicles) is not one of them. The owners manual of the vehicle will inform the owner to bring the car to the dealership for service when a headlight burns out. However, this is not always convenient and is rather costly. Replacing the headlight as a do-it-yourself project is possible, but its going to require a degree of mechanical skill.
Instructions
- 1
Apply the parking brake securely on the 2007 Dodge Caliber with the headlight switch and engine off.
2Lift one front corner of the car with a jack and then lower the jack down onto a jack stand placed under the front frame. Repeat this step for the other front corner to elevate the front axle of the car.
3Turn the ignition key one turn to unlock the steering wheel, and turn the wheel inward away from the respective fender (the drivers side headlight would require turning the wheel all the way to the right and the passenger side headlight would require turning the wheel all the way to the left). Turn the ignition key back to the off position.
4Loosen the screws of the front splash shield/wheel well with the screwdriver. If necessary to reach behind the wheel well, remove a couple of the screws. The wheel well is plastic and somewhat pliable and manageable.
5Shine a flashlight in through the wheel well to locate the headlight electrical connection. The inboard connector is the headlight, while the outboard connector is the parking and directional bulb connector on whichever side (drivers or passenger) the headlight is being replaced.
6Disconnect the electrical connector plug from the socket base of the headlight.
7Turn the socket base of the bulb counterclockwise a quarter turn. Remove the headlight from the lens assembly and extract it through the opening in the wheel well.
8Put on a pair of latex gloves before handling the H13 automotive replacement bulb. Skin oil will compromise the glass bulb of the headlight due to the intense heat it burns at when lit.
9Insert the replacement bulb through the loosened wheel well splash guard and insert it into the lens assembly. Aligning the socket base tabs with the notches in the back of the lens assembly will be required. Use the flashlight to help locate the correct alignment. Turn the socket base of the headlight a quarter turn clockwise to lock it into place and reconnect the electrical connector to the back of the headlight socket base.
10Test the headlight (both low and high beams) before tightening the wheel well screws and lowering the Caliber.
Installing an Oxygen Sensor
Oxygen Detection
The oxygen sensor informs a car computer of the level of oxygen being burned into the fuel. The computer utilizes this information to regulate the mixture of fuel to oxygen. Installing the oxygen sensor in the exhaust manifold allows the amount of O2 in the fuel mixture to be measured. A zirconium ceramic bulb (enameled in a layer of platinum with oxygen holes) is attached to the end of the oxygen sensor (At the end where the sensor is bolted into the exhaust manifold). Two leads platinum electrodes reside inside of the bulb. A very small amount of space is provided for the insulation and the wire. Air must be allowed to reach the oxygen sensor. When installing the oxygen sensor, no grease is used (grease inhibits the flow of oxygen to the sensor).
Heating
At a hot enough temperature the oxygen sensor will produce enough voltage to communicate with the car computer. Typically, the oxygen sensor will include a heating device inside of it. This heating device aids the oxygen sensor by quickly raising the operating temperature (600+ degrees Fahrenheit). Thus a signal to the car computer is produced in a timely manner. Older cars typically have a single lead (wire directly connected to the oxygen sensor) on the oxygen sensor and lack a heating device (operating temperature takes longer to reach). New cars typically possess a self heating oxygen sensor with three or more leads (multiple wires which are directly connected to the oxygen sensor). Over the years, the number of oxygen sensors in any new car has doubled.
Modern Sensor Systems
Modern cars have a second oxygen sensor installed in or behind the catalytic converter. This oxygen sensor monitors converter production. Bigger engines require one oxygen sensor to be installed per cylinder, and an additional oxygen sensor following a catalytic converter. Upstream/ downstream oxygen sensors are installed in many of todays newer cars to monitor emissions performance. This oxygen sensor ensures the converter minimizes pollution (exhaust). Converter failure prompts the malfunction indicator lamp to light up on the dashboard.
Tooling and Wiring
A 22-millimeter socket is used to remove the oxygen sensor from a car. The engine needs to be warmed up just a little bit before removing the oxygen sensor, otherwise the sensor may not budge. The socket is turned counter-clockwise over the bolt holding the sensor in place. Penetrating oil may be used around the bottom of the sensor to help loosen it from its fixture. Wiring on the connector fits all OEM oxygen sensors. Universal oxygen sensors, however, require the wiring connector to be cut. The wires are spliced to connect the connectors wires. Modern sensors typically have four wires (signal, ground, and two wires for the heater circuit. Color coding on a new sensor will not match leads on older converters.
Sunday, March 9, 2014
Troubleshooting a Mazda MPV

Mazdas MPV is a sedan-style car that is perred by consumers for its fuel economy. If you are having problems with your Mazda MPV, there are several things that you can do before you take it to a service shop. Dead batteries, no gas, or a low coolant level can lead to the Mazda MPV not starting. You dont have to be a Mazda technician to get your MPV back on the road. You can generally do it yourself with little hassle.
Instructions
- 1
Turn the key in the MPVs ignition and look over the instrument panel. Check the fuel level and the battery charge to determine if this is your problem. If you hear a clicking noise when your turn the key, you need to have your alternator replaced by a service technician.
2Fill the gas tank with gasoline if needed. Pop the hood to your Mazda MPV and look over the battery connections. The battery is located on the right side of the engine. The battery should be properly connected to the terminals. Use a pair of channel locks to tighten the cable connections to the battery terminals.
3Use a voltmeter to test the battery charge. Hold the leads of the voltmeter to the terminals on the top of the battery. You should get a 12V reading. If you dont get a 12V reading, you can jump the battery.
4Have a friend hook jumper-cables up to their car battery and then connect the other ends of the jumper cable to your cars battery. Start the other car and then try to start your MPV. Allow the battery to charge for about 10 minutes before you turn the MPV off. Try to restart the MPV. If the MPV doesnt restart, the battery is dead and you will need to replace it.
5Check over the coolant system if your MPV is overheating. Locate the coolant tank on the left side of the engine. Look for the fill line on the edge of the tank. Make sure that you coolant is filled to the fill line. If the coolant is not filled to that line, fill it with 50/50 coolant.
The Clifford 6 Cylinder Performance
The Clifford Performance company manufactures parts and accessories to increase the performance of six-cylinder engines to match the performance of larger V-8 engines.
History
Clifford Performance was established as Clifford Research by aerospace engineer Jack Clifford in 1967. Jack Clifford began developing automobile parts because of his interest in drag racing during the 1950s, which he used to increase the performance of a 1954 Hudson Flathead 6 engine.
Performance
To increase the performance of six-cylinder engines produced in the U.S. in the 1960s, Clifford designed modified parts for the intake and exhaust systems, including an exhaust header and intake manifold. These modifications gave six-cylinder engines a similar performance to the larger, more powerful V-8 engines.
Design
Clifford Performance is headquartered in Wildomar, California, where the company manufactures exhaust headers, cams and intake manifolds. Exhaust headers produced by Clifford Performance are created using 16 gauge tubing.
Saturday, March 8, 2014
Audi S3 Common Faults
The Audi S3 is a midsize hatchback family sedan that has been produced by Audi since 1999. The S3 was upgraded in 2006 with a new higher-performance engine, including a new more powerful turbocharger as well as an improved suspension. These upgrades made the S3 one of the highest-performance vehicles in its class. However, like most cars that have been on the market for more than a decade, the S3 does have a number of known faults that can require maintenance or repair.
Water Pump
Earlier models of the water pump on the S3 included a plastic impeller part in the water pump that would eventually fail over time (leading to overheating and potential thermostat damage). This water pump can be replaced with an all-metal water pump.
Heat Shield
The bolts attaching the heat shield between the engine and the passenger compartment are prone to come loose on the S3, leading to a rattling noise. The bolts can usually be easily and inexpensively replaced.
Body Corrosion
Corrosion along the roof rail is a common problem with S3s. The epoxy sealant along weld line joining the roof to the quarter panel weathers over time, allowing water in and leading to corrosion. A respraying of sealant is covered by warranty in vehicles less than 12 years old. The lower trim of the door panel is also prone to rust and corrosion on the S3.
Rear Springs
The rear springs on an Audi S3 are prone to corrosion, especially if you live in a damp place or near the coast. Over time the springs can even break, usually snapping off at the base. These springs are replaceable.
Brake Vacuum Hose
The vacuum pipe connecting the brake servo mechanism to the inlet manifold is manufactured from a hard plastic, which becomes brittle and cracks around the joints as the plastic ages over time from heat cycling. Simply replace the vacuum pipe.
Glovebox Door Hinges
The glovebox door hinges on the Audi S3 will eventually wear out and snap off. Repairing this requires buying and installing a new glovebox assembly.
How to Identify a Borg Warner Transmission

Borg Warner started manufacturing the T5 transmission in 1982. Since its inception, the transmission has been placed into various vehicles, including Ford and General Motors models. The five-speed transmissions fall into two categories: world class and non-world class. The T5 is credited as the only American-made manual transmission to be in production for more than 20 years. The Borg Warner T-10 also is a popular transmission, and both have identifying marks.
Instructions
Finding the Identifiers
- 1
Locate the identification tag number. A quick way to confirm that your transmission is a Borg Warner and what vehicle it was designed for, is to locate the identification number stamped into the "metal tag bolted onto the tail housing," according to 5speeds.com. Once you have the identification number you can access one of the two Web listed in the Resources section of this article to find out more information about the transmission. This listing can tell you what transmission you have and what vehicle it was originally designed for.
2Look at the forward shaft bearing/support. Borg Warner transmissions usually a sticker saying Timken with a part number or a yellow and black sticker that says "use Dexron II only," according to British V8 Newsletter. These stickers are most commonly found on Borg Warner transmissions.
3Count the number of bolts on the transmission cover. On the Borg Warner T10 transmission there are nine bolts attaching the side cover. This is only found on the T10.
4Look numbers on transmission housing. You may not need the entire number stamped on the metal tag to determine whether or not you have a Borg Warner transmission. Knowing what numbers mean Borg Warner might save you a trip to the computer. For example, on a Borg Warner T10, the identifiers T-10 and/or 13-04 should be imprinted on the transmission housing. On a T5, the identifier should begin with 13-52. The casing number on a Borg Warner T19 is 1309and the T18 casing number is 1301. Both the T18 and T19 are "top loaded heavy-duty 4-speed transmissions with [a] cast iron case and shift cover," according to motivegear.com.
Friday, March 7, 2014
Transmission Codes for Chevy Blazers
If your Chevy Blazer is not working correctly, you can use General Motors trouble code numbers to help diagnose the problem. The code numbers are read via a scan tool plugged into the vehicle diagnostic connector under the instrument panel. According to AA1Car, for some code numbers the same number may be used for different faults on different model years or models. After youve figured out the code, further testing must be done before repairs are made, AA1Car warns.
P1500 and P1600 Codes
P1521 is defined as transmission engaged at high throttle angle. P1527 is transmission range/pressure switch comparison. P1623 is transmission temp pull-up resistor.
P1700 Codes
P1700 is transmission MIL request. P1701 is transmission MIL request circuit. P1740 is transmission torque reduction request circuit. P1760 is transmission control module supply voltage interrupted. P1792 is ECM to transmission control module engine coolant signal.
P1800 Codes
P1800 is ECM to transmission control module engine coolant signal. P1812 is transmission over temperature condition. P1815 is transmission range switch-start in wrong range. P1819 is transmission range switch out of range, possible no start. P1820 is transmission range switch A voltage low. P1822 is transmission range switch B voltage high. P1823 is transmission range switch P voltage low. P1825 is transmission range switch A, B, C and P signals invalid. P1826 is transmission range switch C voltage high. P1845 is transmission gear ratio output circuit. P1868 is transmission fluid life. P1870 is transmission component slipping.